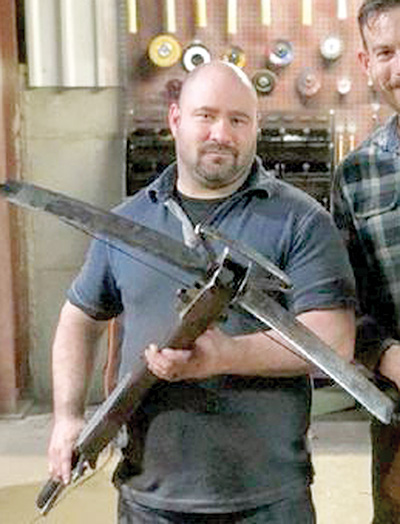
by Tom Chillemi
Nestled just off Main Street in Gloucester’s Historic District is “The Village Blacksmith,” created, owned and operated by George Cramer.
His craft is a throwback to a time when metal was shaped using hand tools and heat.
Here, the senses are greeted by the ring of the hammer on an anvil and the smell of a coal-fired forge as steel is heated red hot, ready to be shaped. It’s the fusion of art and science. His work is sold globally.
Cramer began working with metal before the age 14. It was at his parents’ company that he was first exposed to welding, metal fabrication, mechanical repair and metal art.
Curiosity led him to his first blacksmithing class in 2003 at Peter’s Valley School of Craft in Layton, N.J.
Cramer is a veteran of six years honorable service in the U.S. Navy as a hull technician. He was trained in advanced X-ray quality welding and fabrication on pipe, plate and sheet metal using a diverse array of ferrous and non-ferrous alloys. He also carried out heavy structural welding, cutting and repair functions, brazing, light machining, heavy machinery repair, salvage, search and rescue operations, gas-free engineering and atmospheric testing, CBR defense measures, firefighting and casualty control.
After leaving the Navy in 2009, Cramer worked at a technical college as a welding instructor. He shifted his metal business from part-time to full-time with the creation of The Village Blacksmith LLC in 2015.
He forges a wide array of commissioned and production work from fabrication and welding to traditional blacksmithing, training in the trades, and many other metal crafting functions for both residential and commercial clients.
Cramer is a journeyman welder and has completed two 6,000-hour welding apprenticeships with the U.S. Department of Labor, and the Commonwealth of Virginia. He is a certified welding inspector and a certified welding educator by the American Welding Society. He has a degree in applied marine engineering and is currently working toward a bachelor’s degree in mechanical engineering.
What is the driving force behind The Village Blacksmith?
“It used to be in this country, the product’s quality and durability were the major selling points. Today, focus has shifted to price as the main selling point.
“So, manufacturers make this item as cheap as possible with the least amount of material and lowest overhead. I am so tired of this mass-produced, low-quality, cheaply-made junk!
“Yes, at the end of the day, through what I do, I may be incredibly tired, sore and my hands may be blistered and burned but, I do it to pay tribute to those that came before us, that knew the sacrifices that had to be made to build this great nation.
“I do it for those that will never have the opportunity to do what I do and have done, whether their limiting factors be social, economic or physical. I owe it to them to push forward, to carry on to the best of my ability or I am letting them down.”
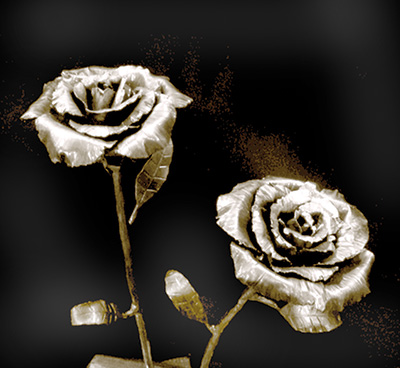
What is the art and science of working metal as a blacksmith?
“What drew me to metal work was the fact you could take something that is seemingly immovable and strong, and manipulate it as if it were clay.
“The ability to work with these materials is boundless. The finished product can be not only functional mechanically but very artistic as well. Blacksmithing is part art, part science, part math, part technology.
“”In the old days a blacksmith not only made his own tools, he made everybody else tools so he had to learn a lot of different skills and learn a lot about different crafts and trades so he could provide quality products to different tradesman. The blacksmith was a major contributor to machine and mechanical design and gave rise to the innovation of many machines that we seen today.”
What satisfaction do you get from creating things using old methods?
“When I am creating items with the forging process, it is almost as if I am in the shoes of those that came before me. The process itself can’t really change that much. You are still hammering steel into a shape and redistributing the mass of the metal, forging is the really the only way you can do that. I am recreating and developing items that others can not do with other means and there is great reverence in that. When I do a restoration or re-creation for someone and they tear up when I deliver it, it is a reaffirmation that I am doing what I am supposed to be doing. Attached to every piece that goes out the door, is a part of someone’s culture, heritage, or it represents something of quality and is of personal significance that is worth having. My customers so often relay how appreciative they are for the work that I do, I feel I am fortunate to experience this in my profession.”
What are some of the more unusual pieces you have crafted?
“We have created some interesting items over the years. Everything from Revolutionary War cannon carriages, to hand forged golf tees, to furniture made from nautical fixtures to brewery and distillery equipment and more recently we worked on the pistols that the main character carried for the 2019 film “Harriet.”
What classes and events are available through The Village Blacksmith?
“We offer one- and three-day basic blacksmithing classes. We are available for private events, team-building workshops, and our most popular experience, Blacksmith Date Night.
“Blacksmith date night comprises a forging experience that involves up to 15 couples and they each get a chance to swing the hammer with the end goal of creating a team project that is given away at the end of the night. Many people come just for the comedy. Others come for the blacksmithing, all leave smiling. We are adding shows currently at local venues like Zoll Vineyards in Gloucester and Eight Shires Distillery in Williamsburg. These experiences pair very nicely with great food and spirits. It is a great time to relax and let loose, it is not a ‘G’-rated event.”
On what TV shows have you appeared?
“I’ve appeared in numerous, news segments and publications from magazines to newspapers.
In 2018 I was a featured craftsman on the Discovery Channel Series: ‘Master Of Arms.’ The task was to make by hand, a steel bow and a crossbow in a competition setting. I was crowned the ‘Master of Arms’ champion and received an award of $10,000.”
Crews for the National Geographic Channel’s “Drain the Oceans” filmed Cramer working at The Village Blacksmith as they researched French armaments used at the Battle of Yorktown to help defeat the British Navy to end the American Revolution.